Blast-resistant structures are common in modern-day industrial settings, protecting, people, equipment and operations alike. Even so, that wasn’t always the case. In a recent BIC Magazine article, Hunter COO Michael Draper offered a look back at where blast resistance began, advances that changed the game along the way — and how Hunter helped our industry take shape. Read on for the full article text:
Safety is king in refinery and industrial plant settings, but it doesn’t rely solely on fall protection and PPE.
When dealing with operations in extreme environments, or those requiring volatile compounds to get the job done, next-level precautions become a necessary part of the conversation.
Blast-resistant buildings are chief among them.
Although common and often required among operations today, blast-resistant technology wasn’t always a “must-have” in the world of oil and gas. Let’s take a look back at how blast resistance got its start, the technology’s current iteration and where the industry is headed.
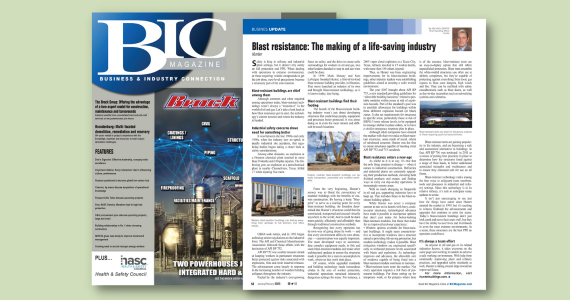
Industrial safety concerns drove need for something better
It was between the late 1980s and early 1990s, when the industry saw an uptick in deadly industrial site accidents, that regulating bodies began taking a closer look at safety considerations.
Among other disasters, an explosion at a Houston chemical plant resulted in more than 20 deaths and 100-plus injuries. The following year, an explosion at a petrochemical plant in nearby Channelview, Texas, killed 17 while injuring five more.
OSHA took notice, and in 1992 began enforcing stricter regulations on the industrial front. The API and Chemical Manufacturers Association followed those efforts with the institution of API RP 752.
API RP 752 was a safety measure aimed at keeping workers in permanent structures better protected against risks associated with explosions, fires and toxic material releases. The advancement came largely in response to the increasing number of wooden building collapses throughout the industry.
Fueled by the industry’s ever-growing focus on safety, and the drive to create safer surroundings for workers in oil and gas, two other leaders decided to step in and see what could be done.
In 1999, Mark Massey and Sam LaVergne founded Hunter, a first-of-its-kind blast-resistant building provider, in Houston. That move launched an industry of its own and brought blast-resistant technology, as it is known today, into being.
Blast-resistant buildings find their footing
The launch of the blast-resistant building industry wasn’t just about developing structures that could keep people, equipment and processes better protected. It was about doing so in even the most remote and difficult-to-reach locations.
From the very beginning, Hunter’s answer was to blend the convenience of modular buildings with the benefits of custom construction. By having a basic “blueprint” to serve as a starting point for every blast-resistant building, the founders determined that Hunter’s structures could then be constructed, transported and erected virtually anywhere in the world. And it could be done more quickly, efficiently and affordably than through traditional construction methods.
Recognizing that every operation has its own way of going about its work – and that every environment offers its own obstacles – customization was equally important. The team developed ways to accommodate complex equipment needs, to link and stack blast-resistant modules and make other architectural updates to ensure the structures made it possible for a team to accomplish its work, wherever that work took place.
Of course, while upgraded standards and building technology made tremendous strides in the area of worker protection, industrial operations remained inherently dangerous settings for many. For instance, a 2005 vapor cloud explosion at a Texas City, Texas, refinery resulted in 15 worker deaths, with more than 180 others injured.
Thus, as Hunter was busy engineering improvements for its blast-resistant buildings, other industry leaders were establishing guidelines aimed at creating a safer overall environment.
The year 2007 brought about API RP 753, a new standard providing guidelines for “allowable building locations” related to portable modules within zones at risk of explosion hazards. Part of the standard’s goal was to establish allowances for buildings within three different explosion hazard (or blast) zones. It also set requirements for structures in specific areas, particularly those at risk of ERPG-3 toxic release levels, to be equipped to manage shelter-in-place orders, or to have a similar emergency response plan in place.
Although other companies have entered the market with their own take on blast-resistant structures, some made of metal, others of reinforced concrete, Hunter was the first to create structures capable of meeting strict API RP 752 and 753 standards.
Blast resistance enters a new age
As cliché as it is to say, it’s true that the only thing constant is change – when it comes to industrial construction. Refineries and industrial plants are constantly upgrading their production methods, elevating both finished products and output, and finding ways to carry out day-to-day operations in increasingly remote areas.
With so much changing so frequently in oil and gas, supporting industries have to keep up. That includes those in the blast-resistant building sphere.
While Hunter was never a company content to rest on its laurels with boxy, cookie-cutter structures, technological advances have made it possible to incorporate updates that don’t just make for better-looking blast-resistant modules, but those that make for an improved end-user experience:
- Window options available for blast-resistant buildings: It might seem counterintuitive to incorporate windows into a structure aimed at providing life-saving protection, but modern technology makes it possible. Blast mitigation windows are engineered specifically to withstand pressure levels associated with blasts and explosions. As technology improves and advances, the allowable size of windows capable of being fitted into a blast-resistant module continues to increase.
- Blast-resistant tents enter the market: Not every operation requires a full fleet of permanent buildings. For those setting up for temporary work, or for projects where time is of the essence, blast-resistant tents are an easy-to-deploy option that still offers unparalleled protection. Blast tents resemble the white-roofed structures you often see at athletic complexes, but they’re capable of protecting against everything from toxic gas ingress to blast zone dangers, high winds and fire. They can be outfitted with safety considerations such as blast doors, as well as day-to-day necessities such as networking systems and cafeterias.
Blast-resistant tents are gaining popularity in the industry, and are becoming a safe and economical alternative to buildings. In fact, API RP 756 was instituted in 2011 as a means of putting best practices in place to determine how the structures fared against a range of blast loads, to better understand associated strengths and weaknesses and to ensure they remained safe for use on all fronts.
Blast-resistant technology ranks among the best ways to safeguard team members, tools and processes in industrial and refinery settings. Since this technology is in its relative infancy, it’s safe to anticipate many updates to come.
It isn’t just encouraging to see just how far things have come since Hunter entered the market in 1999, but it’s exciting to witness firsthand the advancements and upgrades that continue to enter the scene. Today’s blast-resistant buildings don’t just look good and serve their users well, but they have the ability to save lives and livelihoods in even the most extreme environments. In a sense, these structures are the best PPE an operation could have.
It’s always a team effort
As anyone in oil and gas or its related industries knows, it takes everyone on the same page and working in tandem to achieve a safe working environment. With help from continually improving plant and refinery practices, and upgraded safety standards as well, Hunter is taking crucial steps toward an improved future.