Safety is crucial across today’s high-stakes industrial environments, and with the downstream oil and gas sector experiencing record demand and heightened risk, protective infrastructure has never been more important. Custom modular buildings are helping fill that need, delivering tailored, rapidly deployable solutions that protect people, assets and productivity.
In a recent Hydrocarbon Engineering article, Hunter Vice President of Sales Stephanie Wilder discusses ways protective structures are helping downstream operations manage growing health, safety and efficiency challenges — all while supporting evolving production goals. Read the full article below.
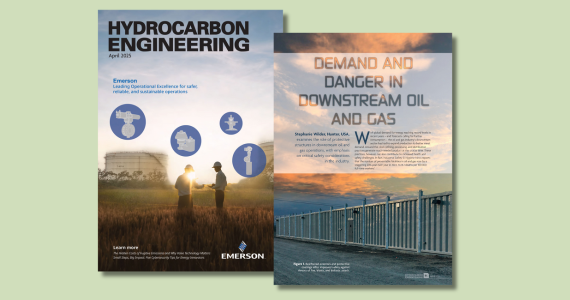
With global demand for energy reaching record levels in recent years – and forecasts calling for further consumption – the oil and gas industry’s downstream sector has had to expand production to better meet demand. Around the clock refining, processing, and distribution practices generate much-needed product at this crucial time. These practices, however, can also contribute to increased health and safety challenges. In fact, Industrial Safety & Hygiene News reports that the number of preventable fatalities in oil and gas rose by a staggering 20% year over year in 2022, to 16.1 deaths per 100 000 full-time workers.1
These sobering statistics underscore the urgent need for safety measures that mitigate risks to downstream personnel, critical systems, and operations. In the last 25 years, custom modular industrial buildings have become essential to industrial safety, providing tailored protection for both lives and livelihoods. This article will explore the risks impacting downstream operations and the role protective structures play in supporting improved safety and operational efficiency.
Understanding the downstream sector’s inherent risks
Jobsite hazards are not theoretical concerns in the downstream sector, they are daily realities. Beyond health and safety concerns, production delays or stoppages can be costly. Some of the unique risks involved include:
Risks to personnel
Workers at downstream facilities are exposed to hazardous chemicals, flammable materials, and the risk of toxic releases which can all produce immense consequences. Refining and processing crude oil involves high-pressure systems, volatile compounds and extreme temperatures, which increases the likelihood of explosions and fires. Additionally, workers face physical injuries related to the handling of heavy machinery and equipment. A single incident can result in life-altering injuries, loss of life, and significant workforce disruptions.
Risks to critical systems and equipment
Efficient and uninterrupted support from control systems, storage tanks, and pipelines is essential for the success of downstream operations. Without suitable protections, these valuable assets become vulnerable to slowdowns, breakdowns, or catastrophic failures. These disruptions can prove costly, not only pausing production, but resulting in considerable repair costs and potential reputational damage. In addition, issues can exacerbate environmental risks, leading to regulatory penalties, and lasting consequences not just for the company, but for the surrounding community.
Securing valuable assets
Engineered to withstand extreme conditions and common hazards, modular protective structures have improved the downstream sector. They not only enable crews to perform critical tasks in hazardous areas but also enhance efficiency with their versatile design.
The combination of protective technology and modular construction techniques allows these structures to deliver cost-effective, customisable solutions to meet the specific challenges of each facility. Studies show that modular builds reach completion approximately 50% faster than those using traditional construction methods – and cost approximately 50% less. They also result in less waste and the finished product can be easily updated or relocated when needs change or initial projects come to an end.
From providing protection for equipment and monitoring systems, to housing control room technology and offering comfortable places for teams to rest between shifts, custom modular protective structures aid all aspects of downstream operations – while supporting consistent communication and production. Common building customisations available in the downstream sector include:
- Air filtration systems which protect personnel and equipment from toxic chemical exposure by maintaining healthy air quality within the structure.
- Fire detection and suppression systems that minimize the risk of fire damage while also supporting emergency response efforts.
- Reinforced exteriors to provide customizable protection against blasts, fires, and threats of forced entry or ballistic attack.
- Blast door integration that offers additional protection against blasts and explosions with engineered designs capable of weathering major events without suffering extensive deformities.
- Integrated communication systems which enable advanced monitoring and real-time communication, ensuring swift action during emergencies and improved efficiency in everyday work.
- Optimised design layouts that enhance efficiency with interiors customised to a company’s workflow, while ensuring safety through strategic designs that support emergency response and swift exits.
Case study
Since 1999, Hunter has enhanced safety across a range of industries, including the downstream sector. The company has provided custom modular solutions for control rooms, living quarters, IT rooms, labs, and guard booths, among other needs. One particular project that highlights these implementations was a large control room that was designed for a technology and automation company.
This 6800 ft2 modular blast-resistant building was engineered to meet the site-specific risks, with key features that addressed complex safety and operational challenges which included:
- Two hour fire protection rating: the control room was engineered to withstand fire exposure for extended periods, ensuring the safety of both personnel and equipment.
- Pre-action sprinkler system: this advanced system minimised fire risks and enhanced emergency preparedness while also minimising the likelihood of water damage in the event of deployment.
- Gas detection systems: continuous monitoring of hazardous gases ensured real-time alerts and rapid response to potential threats.
- Shelter-in-place (SIP) room: the client required a SIP room with an air leakage rate of less than 0.1. Hunter exceeded expectations by designing the entire building to function as a SIP, achieving an exceptional leakage rate of 0.01.
- Specialised epoxy flooring: designed to mitigate radiation absorption, this feature helped to ensure a safer, more resilient workspace while still contributing to its aesthetic.
This project demonstrated how customised modular structures can address complex challenges while still supporting efficient daily operations.
Ensuring future industrial safety with custom modular structures
Just as every downstream operation is unique, so are the specific protection and safety requirements. While finding the right solution is always critical, it becomes even more important during periods of increased production. With the current elevated production rates and the new US Administration’s efforts to further expand the country’s oil and gas output, downstream operations must be strategic about the protections they put in place. Customised protective modular structures offer tailored solutions designed to enhance safety, boost efficiency, and safeguard investments, while keeping costs controlled.
Reference
1. MORRISON, R., ‘Safety first: protecting workers in the oil and gas industry as fatalities and injuries are on the rise,’ https://www.ishn.com/articles/114369-safety-first-protecting-workers-in-theoil-and-gas-industry-as-fatalities-and-injuries-are-on-the-rise, (4 September 2024).