Today’s blast-resistant buildings are tasked with providing more than protection on industrial sites. They house important people and equipment, foster efficient operations and make themselves useful in other parts of a plant once initial projects reach completion. Steel’s versatility and protective qualities make it an ideal building material for such structures.
In her recent BIC Magazine article, Hunter Director of Sales Stephanie Wilder discusses the many benefits associated with steel blast-resistant buildings, and tips for companies working to determine which structures make sense for their needs. Read on for the full article text:
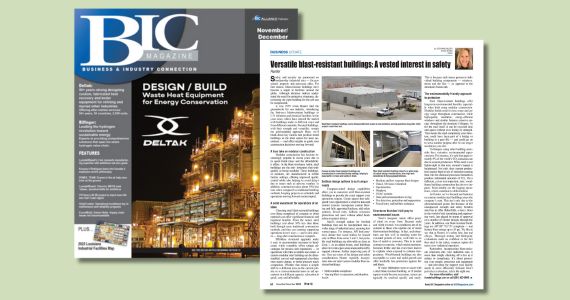
Safety and security are paramount on modern-day industrial sites — for personnel, property and processes alike. For that reason, blast-resistant buildings have become a staple at facilities around the globe.
Although decision makers understand the need for protective structures, determining the right building for the job can be complicated.
It was 1999 when Hunter laid the groundwork for our industry, introducing the first-ever blast-resistant buildings to U.S. refineries and chemical facilities. In the years since, others have entered the market with buildings made in different ways and from different materials. But steel buildings, with their strength and versatility, remain the gold-standard approach. Here, we’ll break down key factors that position metal buildings as the ideal option for most operations — and offer insights to guide your construction decisions moving forward.
A true take on modular construction
Modular construction has become increasingly popular in recent years due to its quick build times and the affordability it offers. In the blast-resistance realm, steel buildings are the only structures that truly qualify as being modular. These buildings, or modules, are manufactured in offsite factory settings, offering improved quality control while also helping to avoid delays due to issues such as adverse weather. In addition, construction takes about 50% less time when compared to traditional building methods, keeping projects on schedule and operations moving forward uninterrupted.
A solid investment for operations of all sizes
Choosing steel blast-resistant buildings over those comprised of concrete or other materials can offer significant financial and logistical benefits. From the outset, steel buildings cost about 50% less than those built through more traditional construction methods, and they can continue supporting operations in new ways — and in new places — long after construction is complete.
Effortless structural upgrades make it easy to accommodate increases in headcount, while versatility offers unique advantages for process unit expansions — or operations with little available real estate. A custom modular steel building can be disassembled, moved and repurposed elsewhere once needs change, or initial projects reach completion. Whether that means a simple shift to a different area on the current jobsite or a cross-continental move to aid operations in a different capacity, relocation is quick, easy and affordable.
Endless design options to suit unique needs
Computer-aided design capabilities allow you to customize steel blast-resistant buildings to provide the exact support your operations require. Create spaces that safeguard your organization’s sensitive data and control systems. Incorporate custom flooring and fully appointed kitchens, add safety systems, forced entry, ballistic resistance protections and more without added headaches or project delays.
Steel’s strength makes for fortified buildings that can be incorporated into a wider range of industrial areas, meaning less wasted space. For instance, API best practices dictate that wood trailers be housed only in Blast Zone areas 2 and 3, but portable steel buildings are allowable as close as Zone 1. As an added bonus, steel buildings allow for wide-open areas unencumbered by support columns, further improving ease of use. Here are some of the design and safety considerations Hunter regularly incorporates into our steel custom modular blast-resistant buildings:
- Multi-module complexes
- Varying blast overpressure and duration levels
- Medium and low response blast designs
- Class I, Division 2 electrical
- Gas detection
- Windows
- HVAC systems
- Data and communications wiring
- Fire detection, protection and suppression
- Forced entry and ballistic resistance
Structures that don’t fall prey to environmental issues
Steel’s inorganic nature offers peace of mind on every front. Because mold can’t feed on steel, wet conditions are of no concern to those who operate out of metal blast-resistant buildings. In fact, such structures can fare well in standing water for extended periods of time, with little to no fear of mold or corrosion. This is in stark contrast to concrete, which retains moisture, becomes brittle and has even been known to explode when exposed to extreme temperatures. Wood-framed buildings are also susceptible to water and mold growth and offer markedly less protection against fire and blasts.
If water infiltration were to occur with a steel blast-resistant building, or if similar repairs would become necessary, issues can typically be resolved quickly and easily. This is because such issues pertain to individual building components — windows, doors and the like — as opposed to the structural framework.
The environmentally friendly approach to protection
Steel blast-resistant buildings offer long-term environmental benefits, especially when built using modular construction. Modular builds result in less waste and energy usage throughout construction, while high-quality insulation, energy-efficient windows and similar features conserve energy throughout the structure’s lifespan. As for the steel itself, it can be recycled time and again without ever losing its strength. That means the steel comprising your structure could have been part of a bridge or building in a past life — and could go on to serve another purpose after it’s no longer needed on your site.
Techniques using other building materials have extensive environmental repercussions. For instance, it’s said that approximately 8% of the world’s CO2 emissions are due to cement production. While steel is not lightweight in that area, cement’s impact is heightened. Not only does cement production require high levels of emission-causing heat, but the chemical processes themselves produce substantial amounts of CO2. On a different, yet no less important, note, woodframe building construction has its own impacts. Most notable are the logging operations, which contribute to deforestation.
At Hunter, we’ve focused our business on custom modular steel buildings since the company’s start. This isn’t only due to the aforementioned points but because of the unsurpassed strength and safety benefits steel has to offer. BakerRisk, a heavy hitter in the world of risk consulting and engineering work, has placed its stamp of approval on a number of Hunter designs through the years. In addition, our blast-resistant buildings are API RP 752/753 compliant — and feature blast ratings up to 10 psi. We like to say that at Hunter, it’s safety first, last and always. Thorough testing and third-party evaluations make us confident in the fact that steel is the safest, smartest option for most every industrial operation.
Remember, incorporating blast-resistant structures into your industrial sites is more than simply checking off a box as it relates to compliance. It’s about protecting your people, processes and equipment — and providing the support your facility needs to move efficiently forward. Don’t just select a structure, select the right one.